In an era where downtime can cripple a production line and cost millions, manufacturers are turning to predictive maintenance powered by artificial intelligence (AI) to stay ahead. Smart factories—those that integrate connected systems and data-driven tools—are now using AI to predict machinery failures before they occur. This helps them avoid expensive repairs, lost production time, and missed delivery schedules.
Unplanned downtime remains one of the largest hidden costs in manufacturing. According to a 2023 Deloitte report, factories lose nearly $50 billion annually due to unexpected breakdowns. But AI-driven predictive maintenance is helping reverse that trend. By using real-time data, machine learning algorithms, and sensor technologies, AI enables maintenance teams to take action before problems spiral.
This blog breaks down how predictive maintenance works, its benefits, and how factories can implement it effectively.
What Is Predictive Maintenance with AI?
Predictive maintenance uses AI and IoT (Internet of Things) sensors to anticipate machine failures before they happen. It’s a smarter alternative to reactive maintenance (fixing something after it breaks) or scheduled maintenance (servicing equipment at set intervals regardless of condition).
Here’s how it works:
- Sensors collect real-time data on temperature, vibration, pressure, and other key indicators.
- Machine learning models analyze patterns in the data to detect early signs of wear or failure.
- Alerts notify maintenance teams to intervene before breakdowns occur.
Unlike traditional systems, AI predictive maintenance continuously learns from new data, improving its accuracy over time.
AI models don’t just use one type of signal either. They blend historical data with real-time performance metrics to form a continuously updating risk profile. This way, engineers can assess whether a machine will likely need attention in the next 5 days or 5 weeks.
Why Downtime Is So Expensive
Downtime not only halts production—it creates a ripple effect across the entire supply chain:
- Production delays
- Missed shipping windows
- Customer dissatisfaction
- Emergency repair costs
- Inventory pile-ups or shortages
And in industries like automotive or electronics, even a few hours of stoppage can result in six-figure losses. This is why predictive maintenance isn’t just a nice-to-have—it’s a competitive necessity.
AI addresses these issues by flagging potential failures early, enabling a shift from reactive firefighting to strategic planning.
Industry 4.0: The Role of AI in Smart Factories
Predictive maintenance fits perfectly into the Industry 4.0 ecosystem. Smart factories rely on interconnected devices and systems that communicate and adapt in real time. AI takes that further by identifying patterns invisible to human operators.
Let’s say a bearing in a packaging unit starts vibrating slightly more than usual. AI systems pick up on this deviation, analyze historical data, and warn the plant manager of a likely failure within 72 hours. This early insight empowers teams to take preventive action without halting the entire operation.
For example, GHzAI systems can analyze motor vibration to detect imbalance or wear. This insight allows engineers to plan maintenance without disrupting operations.
Benefits of AI-Based Predictive Maintenance
✅ Reduces Downtime: Detects problems before they lead to machine failure.
✅ Saves Costs: Cuts emergency repairs and optimizes maintenance schedules.
✅ Extends Equipment Life: Prevents excessive wear, preserving capital assets.
✅ Boosts Productivity: Keeps machines running at optimal performance.
✅ Improves Safety: Identifies risky conditions before they cause accidents.
✅ Supports Sustainability: Reduces waste and unplanned energy usage.
Additionally, predictive maintenance reduces unplanned stoppages, which helps reduce overtime costs, prevents last-minute part orders, and improves overall morale on the shop floor.
Real-World Impact
Several major manufacturers have already seen success with AI predictive maintenance:
- Siemens applies AI to monitor gas turbines, reducing downtime by 30%.
- GE Aviation uses AI to predict engine maintenance needs, saving $10M+ annually.
- Nissan deployed AI to monitor assembly robots and reduced failures by 40%.
- P&G uses AI to keep production lines for household products running with less disruption.
- Multiple industries report up to 50% reduction in unplanned downtime and 40% cost savings on maintenance (McKinsey).
Each of these cases shows how AI’s ability to process massive datasets can translate into operational resilience and business continuity.
Building a Predictive Maintenance Program: Step-by-Step
- Assess Equipment: Identify which machines are critical to operations and prone to failure.
- Install IoT Sensors: Use sensors to track heat, vibration, pressure, etc.
- Select an AI Platform: Choose tools like IBM Maximo, Microsoft Azure AI, or Augury.
- Integrate with Existing Systems: Connect AI outputs to your ERP, MES, or SCADA systems.
- Train Your Team: Ensure staff understands AI alerts and maintenance protocols.
- Start with a Pilot: Run tests on a single line or unit to refine the model.
- Refine and Scale: Improve model accuracy and expand system coverage.
- Monitor ROI: Track savings in downtime, labor hours, and part replacement.
Pro Tip: Start small. A pilot project helps measure ROI and proves the case for broader adoption.
Also, documenting your process and learnings in early phases will help scale effectively later.
Preventive vs Predictive Maintenance
Preventive maintenance is based on usage hours or time intervals. While it’s better than reactive maintenance, it still leads to unnecessary servicing. Predictive maintenance, on the other hand, uses actual equipment condition to guide interventions, reducing unnecessary checks.
This not only saves resources but also avoids wear from over-servicing.
Moreover, predictive maintenance can help reduce technician overload. Rather than wasting time checking healthy machines, they focus only on assets showing real risk signals.
Challenges and How to Overcome Them
No system is without hurdles. Here are common challenges and how to address them:
🔸 Poor Data Quality: Ensure clean, consistent, and accurate data feeds. Garbage in = garbage out. 🔸 Legacy Equipment: Retrofit older machines with IoT devices where possible. 🔸 Skills Gap: Upskill staff or hire AI-savvy technicians and consultants. 🔸 Integration Issues: Choose platforms compatible with your ERP and MES systems. 🔸 Trust in AI: Educate stakeholders on how the system works to build confidence. 🔸 Cybersecurity Risks: Protect IoT networks with robust encryption and firewalls.
In addition, it’s important to create cross-functional teams — IT, operations, and engineering — to manage the rollout and refinement of AI systems.
How AI Actually Predicts Failures
AI doesn’t just guess. It learns. Here’s a simplified breakdown:
- Sensors detect signals like heat, pressure, and vibration.
- Historical data trains the algorithm to recognize what failure looks like.
- The AI model continuously compares current behavior to past patterns.
- Anomalies trigger alerts with recommended actions.
Some systems even provide confidence scores and visual dashboards, helping teams interpret predictions without needing to understand every detail of the algorithm.
The more data the system sees — across environments, conditions, and edge cases — the more precise its predictions become.
Frequently Asked Questions
Q1. Which machines benefit most?
Large, high-impact machines like motors, HVACs, conveyors, injection molders, and turbines.
Q2. Can small plants afford this?
Yes. Scalable platforms and affordable sensor kits make predictive maintenance accessible to SMBs. Cloud-based solutions also reduce upfront infrastructure costs.
Q3. How accurate is it?
With high-quality data and mature models, predictive maintenance systems can reach over 90% accuracy. The key is consistent calibration and retraining.
Q4. How long does implementation take?
Pilots can be launched in 4–6 weeks. Full deployment across a facility may take 3–6 months depending on complexity.
Q5. Do I need a data scientist to run this?
Not always. Many platforms offer no-code interfaces. However, having someone on the team with analytics or AI knowledge improves performance.
A Safer, Smarter Future
“Predictive maintenance with AI isn’t a trend — it’s the future.”
That quote summarizes what many industry leaders now believe. With AI, smart factories are moving from reactive to proactive, achieving new standards in uptime, efficiency, and safety. The sooner you adopt this approach, the sooner you’ll see benefits.
As regulatory bodies and supply chains increasingly demand proof of resilience and uptime performance, predictive maintenance will become not just valuable—but mandatory.
Final Thoughts
If your factory still runs on a reactive or scheduled maintenance model, you’re leaving efficiency—and money—on the table. Predictive maintenance powered by AI is your chance to upgrade operations, protect assets, and reduce costs.
The transition doesn’t have to be overwhelming. Begin with one machine, one line, one team. Let the data guide you.
In the competitive world of manufacturing, speed and reliability are king. And predictive maintenance helps you master both.
Because in the world of manufacturing, the smartest future is the one that doesn’t wait for problems to occur.
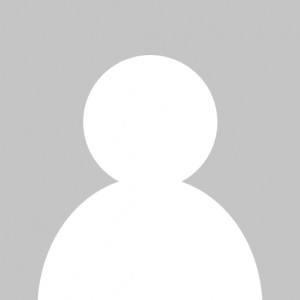
Passionate about breaking down complex tech into simple ideas. Covers everything from AI and software development to gadgets and emerging tech trends.