It all started with the mechanization and the use of steam to power those machines that change the manufacturing industries for the first time. This advancement allowed factories to set up mass production and assembly lines. This was the time that electricity came in the equation.
Over the years along with technological advancements computers and automated machines were created to take the workload of the assembly line. Industry 4.0 advances the trend of automation through digitization and network production with cyber-physical systems and the cloud computing industry 4.0 creates a smart factory.
Following are the Technological Advancements in Manufacturing 4.0
1. Cyber Security
In industry 4.0 the connectivity of the flow of information is raising the concerns about security transparency and privacy as the practices in manufacturing are increasingly becoming personal and customizable.
The appeal of the company gets hugely influenced by the data management practices either done outside or within the shop floor. To avoid cyber-attacks on critical industrial facilities’ digital ethics and privacy the processing and transmission of sensitive industrial data need to be done safely.
Privacy-enhancing technologies, self-adaptive security, zero-trust security, end-to-end communication security, and blockchain technology are some of the new developments on this front. The focus on cyber security needs to be balanced with transparency and privacy.
2. Cloud Computing
The immense amount of data being generated by the industrial internet of things is propelling the adoption of edge, fog, and cloud computing capabilities in industry 4.0. Clouds, distributed clouds, distributed compute and storage, hybrid computing, low code development platforms, microservices, mobile computing, and multi-access edge computing are connected by custom hardware and software solutions that are shaping this industry 4.0 trend.
3. Artificial intelligence
Innovations have been driving across industries and functional areas through the implementation of AI and machine learning. To optimize the existing systems and tackle new challenges facing manufacturing artificial intelligence-specific hardware and new algorithms are being developed.
The integration of AI across their production systems and processes has been started by factories. To conduct predictive maintenance, cognitive computing, swarm intelligence, context-aware computing, smart machines, hardware accelerators, and generative design become possible by advanced AI making it possible for all of these technologies to propel manufacturing facilities to move towards complete lights out manufacturing.
4. Human augmentation and extended reality
The physical and cognitive augmentation of humans forms another major industry 4.0 trend the limitations in humans are being augmented with the help of technologies such as variables and exoskeletons. XR technology like mixed reality augmented reality and virtual reality are already in use in industry 4.0 from research and development to full-scale production and post-production processes.
This multi-experience paradigm is changing the way industrial manufacturing systems function the nature of human-machine interaction is aligning mode toward machine-enabled workers.
5. Network and Connectivity
Network and connectivity are among the main driving forces in enabling industry 4.0 a number of technology development such as edge to cloud gigabit ethernet Networks low power wide area networks. 5G machine-to-machine communication real-time ethernet time-sensitive networking radio access unified IoT framework and zero-touch networks.
Nudge factories to implement it to transform into industry 4.0 facilities, these technologies constantly improve machines and human-machine communication as well as data transmission as a result innovation in this area increases speed, improves security and efficiency, and reduces the cost of network connectivity.
Conclusion
To sum up, the above-mentioned technologies are not the only technologies involved in manufacturing 4.0 there are more to it. This technology trend leads to making the industrial revolution 4.0 flourish and increases the productivity of many businesses.
Are you looking to implement digital twins technology into your manufacturing business? If yes so please feel free to contact us at support@aeologic.com
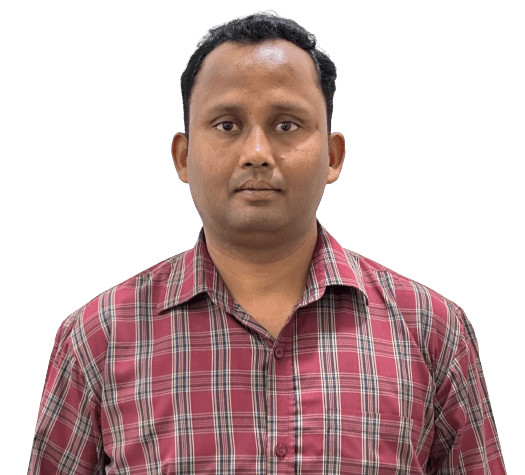
Manoj Kumar is a seasoned Digital Marketing Manager and passionate Tech Blogger with deep expertise in SEO, AI trends, and emerging digital technologies. He writes about innovative solutions that drive growth and transformation across industry.
Featured on – YOURSTORY | TECHSLING | ELEARNINGINDUSTRY | DATASCIENCECENTRAL | TIMESOFINDIA | MEDIUM | DATAFLOQ